In industrial settings where the risk of fires can have devastating consequences, the importance of reliable fire suppression systems cannot be overstated. From manufacturing plants to data centres, these specialized systems play a crucial role in safeguarding lives, property, and business operations. In this blog post, we will explore the different types of industrial fire suppression systems, how they work, their various applications, and the essential maintenance practices to ensure their effectiveness. Join us as we delve into the world of industrial fire suppression systems and uncover the key information you need to know to protect your workforce and assets.
Introduction to Industrial Fire Suppression Systems
Industrial Fire Suppression Systems are specialised installations designed to detect and suppress fires in industrial environments. These systems are crucial for preventing the spread of fires and minimizing the potential damage to property, equipment, and personnel. By combining advanced detection mechanisms with effective suppression agents, industrial fire suppression systems provide a proactive approach to fire safety.
The primary goal of industrial fire suppression systems is to detect fires at their early stages and initiate a rapid response to control and extinguish them before they can escalate. These systems are tailored to specific industrial applications, considering factors such as the nature of the materials used, the scale of operations, and the potential fire hazards present.
In the following sections, we will explore the different types of industrial fire suppression systems, their working principles, and their applications in various industrial settings. Understanding these systems is essential for businesses to make informed decisions regarding the most suitable fire suppression solution for their specific needs. Let’s dive into the world of industrial fire suppression systems and discover the diverse range of options available to protect your valuable assets.
Different Types of Industrial Fire Suppression Systems
Industrial fire suppression systems come in various types, each designed to address specific fire hazards and environments. Understanding the different types of systems available is crucial for selecting the most appropriate solution for your industrial setting. Let’s explore the main categories of industrial fire suppression systems:
1. Water-Based Fire Suppression Systems:
Water-based fire suppression systems are the most common and widely used type of fire suppression system. These systems utilise water as the primary extinguishing agent to control and extinguish fires. They are effective for combating Class A fires, which involve ordinary combustible materials such as wood, paper, and cloth.
Some common examples of water-based fire suppression systems include:
- Sprinkler Systems: Sprinkler systems are widely used in industrial settings and operate by automatically releasing water when the heat from a fire activates a sprinkler head. These systems are highly effective in controlling fires and preventing their spread.
- Water Mist Systems: Water mist systems discharge a fine mist of water droplets to suppress fires. The mist helps cool the fire and displace oxygen, reducing the heat and suffocating the flames. Water mist systems are suitable for areas where water damage needs to be minimized, such as data centres or sensitive electronic equipment rooms.
2. Gas-Based Fire Suppression Systems:
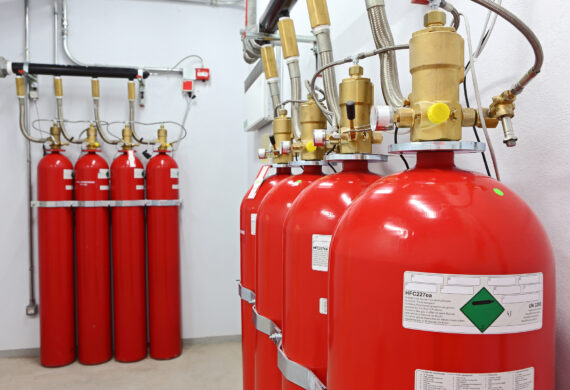
Gas-based fire suppression systems employ various gases to suppress fires by reducing the oxygen concentration or interrupting the chemical reaction that sustains the fire. These systems are particularly useful in environments where water may cause damage or where rapid evacuation is necessary. Some common examples of gas-based fire suppression systems include:
- Halon Systems: Halon systems were widely used in the past but are now being phased out due to environmental concerns. Halon gas is highly effective in suppressing fires by chemically reacting with the fire, interrupting the combustion process. However, alternative clean agents have replaced Halon systems in most applications.
- Inert Gas Systems: Inert gas systems, such as Argon and Nitrogen, work by reducing the oxygen concentration in the protected area. By displacing oxygen, the fire cannot sustain itself. These systems are commonly used in areas where valuable assets need protection, such as server rooms and archives.
- CO2 (Carbon Dioxide) Systems: CO2 systems are effective in suppressing fires by displacing oxygen and inhibiting the combustion process. They are commonly used in areas where water can cause damage or in environments with electrical equipment, such as server rooms, control rooms, and electrical switchgear rooms.
3. Foam-Based Fire Suppression Systems:
Foam-based fire suppression systems are designed to combat flammable liquid fires, also known as Class B fires. These systems discharge a foam mixture that covers the fuel surface, forming a barrier between the fuel and the oxygen in the air. This barrier suppresses the fire by preventing the release of flammable vapours and cooling the fuel surface. Foam-based systems are commonly found in industrial settings where flammable liquids are stored or processed, such as refineries, chemical plants, and fuel storage facilities.
4. Dry Chemical Fire Suppression Systems:
Dry chemical fire suppression systems are effective for suppressing a wide range of fires, including Class A, B, and C fires. These systems discharge a dry chemical agent, such as monoammonium phosphate or potassium bicarbonate, onto the fire, interrupting the chemical reaction and extinguishing the flames. Dry chemical systems are commonly used in industrial environments where multiple fire hazards are present, such as manufacturing facilities, warehouses, and paint booths.
Understanding the different types of industrial fire suppression systems is essential for selecting the most suitable solution based on the specific fire risks present in your industrial setting. In the next section, we will explore how these systems work to detect and suppress fires effectively.
How Industrial Fire Suppression Systems Work
Industrial fire suppression systems employ a combination of detection mechanisms, activation systems, and suppression agents to effectively detect and suppress fires. Understanding how these systems work is crucial for ensuring their reliable operation in case of a fire emergency. Let’s explore the key components and working principles of industrial fire suppression systems:
1. Detection Systems:
Detection systems are responsible for identifying the presence of a fire and initiating the necessary actions for fire suppression. There are various types of detection systems used in industrial fire suppression systems, including:
- Smoke Detectors: Smoke detectors are commonly used in fire suppression systems and are designed to detect the presence of smoke particles in the air. When smoke is detected, the system is triggered to initiate the fire suppression process.
- Heat Detectors: Heat detectors are designed to sense the temperature rise caused by a fire. They can be either fixed temperature detectors, which activate when a specific temperature threshold is reached, or rate-of-rise detectors, which activate when the temperature rises rapidly within a short period.
- Flame Detectors: Flame detectors are optical sensors designed to detect the presence of flames by sensing the ultraviolet (UV), infrared (IR), or both UV and IR radiation emitted by the fire. When flames are detected, the system is alerted and activates the fire suppression process.
2. Activation Systems:
Once a fire is detected, the activation systems are responsible for initiating the fire suppression process. The activation systems can be manual or automatic, depending on the specific requirements of the industrial setting. Some common activation systems include:
- Manual Activation: Manual activation systems require human intervention to initiate the fire suppression process. This can be done through the use of manual pull stations or buttons placed at strategic locations, allowing personnel to manually activate the system when a fire is detected.
- Automatic Activation: Automatic activation systems are designed to initiate the fire suppression process automatically when specific conditions are met. For example, when smoke is detected or when a certain temperature threshold is exceeded, the system triggers the activation of the suppression agents.
3. System Discharge and Fire Suppression:
Once the fire suppression system is activated, the suppression agents are discharged to control and extinguish the fire. The type of suppression agent used depends on the specific fire hazards and the type of fire suppression system installed. Some common suppression agents include:
- Water: Water-based fire suppression systems rely on water as the primary suppression agent. When activated, water is discharged through sprinklers, water mist nozzles, or other delivery mechanisms to cool the fire, remove heat, and extinguish the flames.
- Gas: Gas-based fire suppression systems utilize specialized gases, such as inert gases or CO2, to suppress fires. When discharged, these gases reduce the oxygen concentration, interrupting the combustion process and extinguishing the fire.
- Foam: Foam-based fire suppression systems discharge a mixture of foam concentrate and water to form a foam blanket over the fuel surface. This foam barrier separates the fuel from oxygen, suppressing the fire and preventing its spread.
- Dry Chemicals: Dry chemical fire suppression systems discharge dry chemical agents onto the fire. These chemicals interfere with the chemical reaction of the fire, interrupting the combustion process and extinguishing the flames.
Once the fire is suppressed, the system may continue to operate to ensure the fire is fully extinguished, or it may enter a standby mode to monitor the area for any potential re-ignition.
Understanding the working principles of industrial fire suppression systems allows businesses to make informed decisions regarding the installation and maintenance of these critical safety systems. In the next section, we will explore the various applications of industrial fire suppression systems in different industrial settings.
Applications of Industrial Fire Suppression Systems
Industrial fire suppression systems have a wide range of applications across various industrial settings. These systems are designed to address specific fire hazards and protect critical assets, ensuring the safety of personnel and minimizing potential damage. Let’s explore some common applications of industrial fire suppression systems:
1. Applications in Manufacturing Industries:
Manufacturing industries often involve processes that generate heat, sparks, or flammable materials, making them prone to fire hazards. Industrial fire suppression systems are essential in these environments to prevent fires from spreading and causing significant damage. Some specific applications include:
- Factory Floors: Industrial fire suppression systems are installed in factories to protect production lines, machinery, and storage areas. These systems help control fires that may arise from equipment malfunction, electrical faults, or flammable materials used in manufacturing processes.
- Paint Booths: Paint booths used in automotive, aerospace, or other industries require specialized fire suppression systems. These systems are designed to suppress fires caused by flammable paints, solvents, or combustible dust particles present in the paint booth environment.
- Chemical Processing Plants: Chemical processing plants handle hazardous materials and involve various processes that can lead to fires. Industrial fire suppression systems are crucial in these facilities to protect personnel, prevent explosions, and minimize the damage caused by chemical fires.
2. Applications in Warehousing and Storage Facilities:
Warehouses and storage facilities often store large quantities of flammable materials, making them susceptible to fire incidents. Industrial fire suppression systems play a vital role in safeguarding these facilities and minimizing the risk of fire-related losses. Some common applications include:
- Bulk Storage Areas: Industrial fire suppression systems are installed in bulk storage areas, such as warehouses or distribution centres, to protect stored goods, pallets, and racks. These systems help control fires that may originate from electrical faults, overheating equipment, or flammable materials stored nearby.
- Cold Storage Facilities: Cold storage facilities, including refrigerated warehouses and freezers, require specialized fire suppression systems to address the unique challenges posed by low temperatures. These systems are designed to suppress fires while considering the impact on temperature-sensitive products and the potential for water freezing.
3. Applications in Commercial Kitchens:
Commercial kitchens, such as those in restaurants, hotels, or catering facilities, are prone to fires due to the presence of open flames, hot cooking surfaces, and grease buildup. Industrial fire suppression systems are crucial in these environments to protect personnel, prevent fire spread, and minimize property damage. Some specific applications include:
- Kitchen Hoods and Exhaust Systems: Industrial fire suppression systems are installed in kitchen hoods and exhaust systems to suppress fires originating from cooking equipment, such as stovetops, grills, or fryers. These systems quickly detect and suppress fires before they can spread to the surrounding areas.
- Ductwork Protection: Ductwork protection systems are designed to suppress fires that may occur within the ventilation ducts of commercial kitchens. These systems prevent fire spread through the ducts, reducing the risk of extensive damage and allowing for safe evacuation.
4. Applications in Data Centers:
Data centres house critical IT infrastructure and sensitive electronic equipment that can be vulnerable to fire incidents. Industrial fire suppression systems are essential in data centres to protect valuable data, prevent equipment damage, and ensure business continuity. Some specific applications include:
- Server Rooms: Server rooms within data centres require specialized fire suppression systems to suppress fires without causing damage to critical equipment. These systems are designed to use gas-based suppression agents, such as inert gases or clean agents, to extinguish fires without leaving residue or water damage.
- Electrical Equipment Rooms: Fire suppression systems are installed in electrical equipment rooms to protect switchgear, transformers, and other electrical components. These systems are designed to suppress fires caused by electrical faults while considering the unique hazards associated with energized equipment.
Industrial fire suppression systems have diverse applications in various industrial settings, and their implementation is essential for ensuring the safety of personnel, protecting valuable assets, and minimizing potential losses. In the next section, we will explore the maintenance practices necessary to keep these systems in optimal working condition.
Maintaining Industrial Fire Suppression Systems
Maintaining industrial fire suppression systems is crucial to ensure their reliability and effectiveness in the event of a fire emergency. Regular inspection, testing, and maintenance practices are essential to keep these systems in optimal working condition. Let’s explore some key maintenance practices for industrial fire suppression systems:
1. Regular Inspection and Testing:
Regular inspections and testing help identify any potential issues or malfunctions in the fire suppression system. Here are some important maintenance practices to consider:
- Visual Inspections: Regular visual inspections should be conducted to check for any visible signs of damage, corrosion, or obstructions that could hinder the proper operation of the system. This includes inspecting pipes, nozzles, detection devices, and control panels.
- Functional Testing: Periodic functional testing should be performed to ensure that all components of the fire suppression system are functioning properly. This includes testing the activation systems, detection devices, and suppression agents to ensure they operate as intended.
- Alarm and Communication Testing: Testing the alarm and communication systems associated with the fire suppression system is essential to ensure that alerts and notifications reach the appropriate personnel or monitoring centres.
- Documentation and Record-Keeping: Maintaining proper documentation and records of inspections, testing, and maintenance activities is important for compliance purposes and to track the system’s performance over time. This includes documenting any repairs or replacements carried out.
2. Routine Maintenance:
Routine maintenance practices help ensure the longevity and reliability of industrial fire suppression systems. Here are some important maintenance practices to consider:
- Cleaning and Lubrication: Regular cleaning and lubrication of system components, such as valves, actuators, and control panels, help prevent corrosion, ensure smooth operation, and extend the life of the system.
- Filter Replacement: If the fire suppression system includes filters, regular replacement or cleaning of these filters is necessary to maintain proper airflow and prevent blockages that could affect the system’s performance.
- Battery Maintenance: If the fire suppression system includes batteries for backup power, routine maintenance should include checking the battery condition, testing their functionality, and replacing them as needed to ensure reliable operation during power outages.
- Suppression Agent Replenishment: If the fire suppression system utilizes suppression agents such as foam concentrates or dry chemicals, it is essential to periodically check and replenish these agents to ensure they are at the appropriate levels for effective fire suppression.
3. Compliance with Safety Standards:
Industrial fire suppression systems must comply with relevant safety standards and regulations. Ensuring compliance helps to maintain the system’s effectiveness and mitigate potential risks. Here are some important considerations:
- Regular Inspections by Certified Professionals: Engaging certified professionals for regular inspections and maintenance of the fire suppression system ensures compliance with safety standards and regulations. These professionals are trained to identify and address any issues that may impact the system’s performance.
- Adherence to Manufacturer’s Guidelines: Following the manufacturer’s guidelines for maintenance, inspection intervals, and recommended procedures is crucial to maintain the system’s compliance and effectiveness.
- Updates and Upgrades: Keeping up with advancements in fire suppression technology and industry standards is important. Periodically reviewing the system’s design and considering updates or upgrades can enhance its performance and align it with the latest safety requirements.
By implementing regular inspection, testing, and maintenance practices, businesses can ensure that their industrial fire suppression systems are well-maintained, reliable, and ready to effectively suppress fires when needed. Proper maintenance not only protects life and property but also provides peace of mind knowing that the fire protection measures are in optimal working condition.
In conclusion, industrial fire suppression systems are vital components of fire safety in various industrial settings. Understanding the different types of systems, their working principles, applications, and maintenance practices is crucial for businesses to make informed decisions and ensure the safety of their workforce, protect valuable assets, and minimize potential losses in the event of a fire emergency.